Radios Help Stamp Out Downtime on Auto Press
The problem
Two transfer presses at a plant had been causing a ruckus. At least once a quarter, the hardwired network suffered cable degradation, and each occurrence caused the entire operation to shut down for up to two hours. Something had to be done.
The two presses produced up to 1,800 parts per hour. The presses were hardwired and faced frequent downtime from cable breakage or damage, frustrating the team on the plant floor.
It cost Gestamp approximately $14,500 each time they had to replace the RG-6 coaxial cable, plus the value of the 1,500-2,400 parts that could not be produced during the outage. They’d see this process play out about every 2 to 3 months per press.
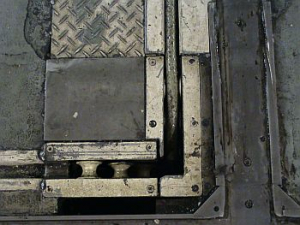
The Application
Each press consists of one ram, two dies, and two bolsters. The bolsters are mobile metal plates on which the dies are mounted. A die is used as a mold that defines the shape that the part will take. In this application each die is roughly the size of a one-ton pick-up truck.
During the process, a metal sheet is fed across one bolster and comes to a rest above the dies. The ram rises and drops with a force of 800 to 1,400 metric tons, sandwiching the metal sheet between itself and the die to stamp out the parts. While one of the bolsters stamps parts, the second is loaded.
The Challenge
The cable wasn’t as much the problem as the demands placed on it. The cable’s path ran along a corner that required it to achieve such a sharp angle that the cable inevitably wore in this area.
Nevertheless, the end user needed a more reliable network, but there was a question about whether a wireless system would be effective given that wireless points would need to be affixed in a partially obstructed location beneath the bolsters.
The Solution
The company spoke with the local Rockwell Automation® distributor, who recommended using six Frequency Hopping Ethernet radios from ProSoft Technology, along with the end user’s existing ControlLogix® PACs.
ProSoft Technology’s Strategic Product Manager for Wireless Technologies said, “When the direct path (line-of-sight) is obstructed, a signal will reflect off of other objects, taking an alternate path to the receiving radio. Because there are multiple reflections, the signals arrive at the receiving radio at different times, so the radio needs to be able to distinguish between the different signals. ProSoft Technology’s Frequency Hopping radios are able to work with reflected signals because of the narrow band ‘hops’ and changing frequencies, making them less impacted by multipath interference compared to higher-speed, wider-band technologies such as 802.11.”
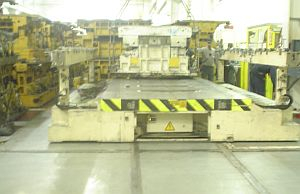
The Wireless Network
Each press is automated by a dedicated ControlLogix. To replace the hardwired system, four FLEX™ I/O ControlNet™ communication adapters — one for each bolster — were replaced with EtherNet/IP™ adapters and an Ethernet radio. Each PAC was fitted with a second 1756-ENBT Ethernet card and an Ethernet radio.
Performance
“We’ve got a unique application here, involving large moving hunks of steel. Our initial concerns that the steel would impede the radio performance turned out to be unfounded. When the bolsters interfere with line-of-sight, the radios continuously try to read through the bolsters,” a representative for the end user said.
This specific application shows that though the laws of physics cannot be changed, the obstacles they present can be circumvented when armed with the right technology: in this case, a high-quality industrial wireless solution. By using ProSoft Technology’s Industrial Frequency Hopping radios, the end user has been able to eliminate the downtime plaguing its facility, translating into a savings of up to $174,000 per year, plus the value of parts produced during that time. The wireless system has been live for a while now and the end user is still pleased with the performance of the radios. “In fact, the radios work better than expected. We’ve been very happy with them.”
Learn more about ProSoft Technology’s Wireless Solutions here.